Our Story
Buckland Timber is the largest manufacturer of glulam in the UK.
At our home in Devon, our team of designers, structural engineers, project managers, carpenters and joiners all work under one roof to design, manufacture and install bespoke glulam structures.
We provide glulam for the broadest range of project needs, from a single beam to the design, manufacture and installation of equestrian sized arenas.
If you are considering glulam for a project, give us a call and a Buckland Timber engineer or designer will be delighted to chat over your ideas with you.
Company History
Buckland Timber Ltd was established in 2012. The partnership was set up by Bill Blight and Ralph and Robin Nicholson with the purpose of producing a British grown and manufactured alternative to glulam imported from Europe.
Bill Blight ran a small sawmill at Buckland Wood, North Devon until the late 1990s, and it’s this link that gave our company its name, Buckland Timber. We have used larch timber from Buckland Wood which Bill claims to have planted in the 1960s. Long-term planning indeed!
Our Managing Director, Robin Nicholson, has a background as a structural engineer and project manager prior to starting Buckland Timber. This experience enabled the company to develop a turnkey design, manufacture and install service, utilising both the British grown and imported timber as appropriate to the project.
Over the years, we have developed into a team of designers and makers with a unique capacity for the in-house design and manufacture of bespoke glue-laminated timber in the UK.


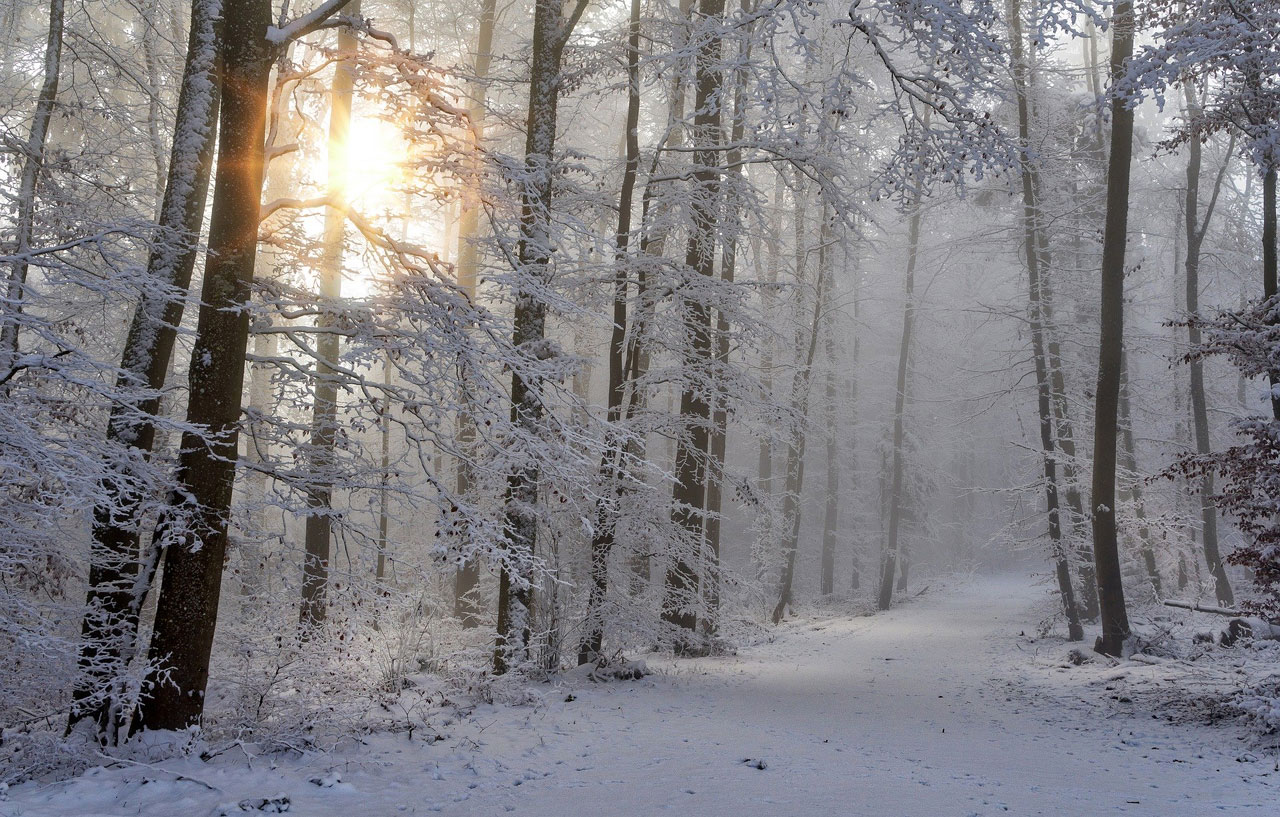
Buckland Turns Ten!
In 2023 Buckland Timber officially celebrated our 10th anniversary in business. We decided to take a moment to celebrate this milestone with the people who made this possible, inviting friends, colleagues and family to join us in person at our factory in Crediton.
The celebration included an open house where you could take a tour of the factory, and we showcased favourite projects, explained the production process and also took a moment to pause and reflect on how far we’ve come.
If you missed the event and would like to come and visit us, do get in touch and we can arrange a time to show you around.

Read our 10 year articles…
Buckland Timber Fun Facts (from our 10 year celebration open day)

1
At our current production rate, we are using 15000 litres of glue per year, this equates to 75 full baths of glue.

2
Up until 2020 the whole Finger jointing line was controlled by a 1980’s computer with a floppy disc drive (pre windows)

3
We have graded Approximately 5600m³ of timber through this position. This Timber placed on a football pitch would be 1.2m tall.

4
During the Kiln Drying process the timber can shrink by up to 10% of its original size.

5
The offcuts that are produced at this station are then Burned in our boiler this generates around 76,000 KW of energy a year

6
Around 500,000 finger joins have been cut since we started

7
The Glue reservoir is cooled to extend the pot life of the glue, we use a farm milk tank refrigerator unit to achieve this.

8
The force that is needed for a 100 x 50 timber is similar to the estimated bite force of a large 6.7m adult Saltwater Crocodile

9
746km of timber has passed through this planer since we started. These laid end to end would reach from the factory to Inverness

10
124,000 laminations have been removed from the Fj line

11
The formaldehyde given off by the glue once cured is similar in quantity to that, that is given off naturally by the timber

12
The battery impact wrench can produce 1050Nm of torque

13
Setting the clamps can take from 1 hour to 8 hours depending on the complexity of the curve.

14
300kw of energy is used per night to cure the glulam, this would be similar to the energy used to run an average UK home for 6 weeks

15
The planer can take a single beam 1600mm wide and 320mm thick and can plane 15mm from the top and bottom faces and 20mm from both sides in 1 pass.